iSwarf 550 - 15
Briquette diameter
Pump input
Output
Hopper
Pressure
Outside working temeprature
Allowed dimension of input material
Dimensions
60-100 mm
15 kW
130-600 kg/h
to 0,75 m3
130 - 280 МPа
from +5 to +35 °C
to 30 mm
2300 x 2160 x 1630 mm
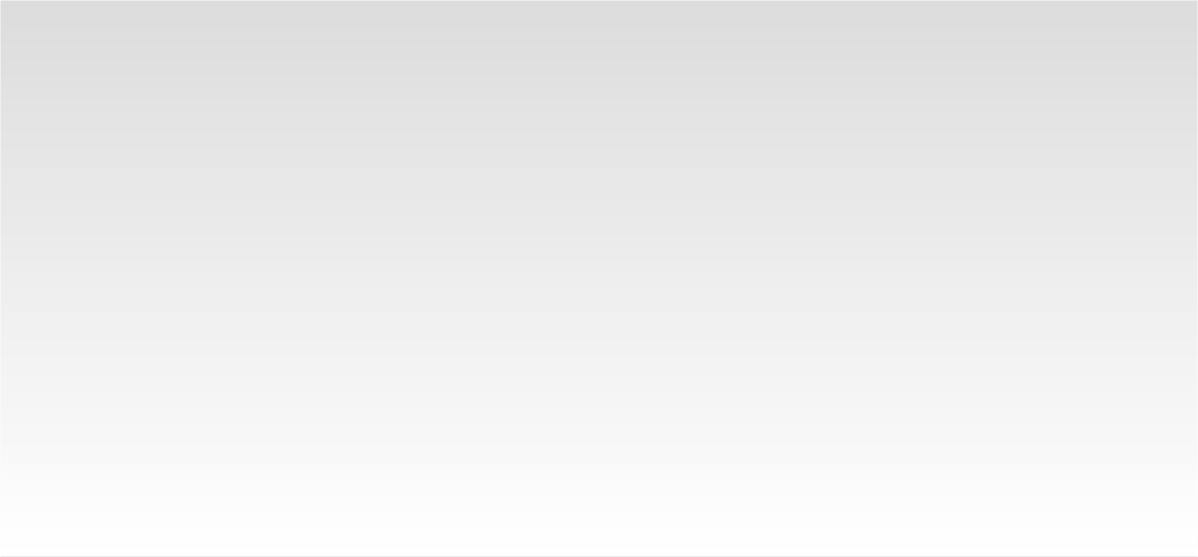
Economical advantages
Technology of briquetting metal chips brings profit by the lowering looses during recycling of chips and minimalize costs of manipulations and storage. Chips from machining are valuable resource which must be handled economically as the starting material. Present metal working production is affected by the growing international competition which make a pressure to lowering producing costs and product prices. By using briquetting press for chip processing offers very good possibility of economical solution. High specific weight of briquettes allows their melting with very low loose of metal. Return of invest to the briquetting presses for metal chips is approximately untill one year, depends on economical conditions per country.
By the briquetting of metal waste you can lower their amount around 8x, the cost of briquetted waste transportation and storage is much lowered.
Re-using of cooling fluid from machining
Every briquetting press is equiped with cooling fluid separator in standart, which is in specified amount evacuated from the machine with chips by chip conveyor. After separation of liquid from chips the liquid goes through the sieve for catching other dirts contained in liquid from machining. After that cooling liquid can be reused in machining centre without any other treatments. also if it is required cooling liquid can go from press through paper filtration if machining centre is equiped with it.
Benefits of briquetting technology
+ Direct connection to the producing line, easy operation, quick service
+ Maximal squeezing of material in all amount of briquettes
+ Possibility of change more suitable hopper regarding to change of conditions of production
+ Partial compensation of crusher for chip before briquetting
+ Partial compensation of centrifuge, low residual humidity
+ Tanks for catching cooling liquid separated from chips after machining
+ Integrated trough for briquette evacuation
+ GSM module managing reports about machine status through SMS message
+ Spare of storage spaces for chips and lowering of their amount
+ Lowering the cost of material manipulations, higher safety of manipulation
+ More economical and more safe of briquette melting thanks to smaller surface
+ Lowering the dust catching in filters a lower producing of slag
Benefits
aluminium
cast-iron
steel
other materials
Your sample
?
Materials suitable for briquetting
Output
around...………... 500 кg/h
(Output depends on detailed specific of the material, briquetting test is all time recommended)
Output
around...………... 550 кg/h
(Output depends on detailed specific of the material, briquetting test is all time recommended)
Output
around...………... 550 кg/h
(Output depends on detailed specific of the material, briquetting test is all time recommended)
If you want to briquette any other material we will conduct a free test after receiving a sample of material weighing at least 50 kg
copper
brass
grinding sludge
lead
Output kg/h
by the briquette test results
Output kg/h
by the briquette test results
Output kg/h
by the briquette test results
Output kg/h
by the briquette test results
Available hoppers for presses iSwarf
Regarding to properties of briquetting material and possible way of dosage we will recommend you optimal type of hopper from this variants:
+ hopper type 4 - basic with dimensions 200 x 400 mm and with screw conveyor
+ hopper type 6 bigger with dimensions 600 x 1000 mm and with screw conveyor
+ hopper type 12 with square bottom 1200 x 1200 mm with balancing mill and screw conveyor sealed against escape of liquids
+ hopper type 3SN-12 with three screw conveyors and volume 0,6 m3 with chain drive and pressing cylinder WA suitable for pressing longer chips
+ hopper type 4SN-12 with four screw conveyors and volume 0,75 m3 with chain drive and pressing cylinder WA suitable for pressing longer chips
Optimal hopper we will recommend you regarding producing conditions
Options
Options
+ Sensors for guarding the amount of chips in hopper which allows automatic managing of process and managing external conveyor transporting chips to the hopper
+ Connecting of GSM module managing reports about machine status through SMS message for more user friendly operations
+ Hydraulic oil for temperatures lower than + 5 °C, using this oil allows using press in conditions of cold hall or outside to the temperature of -15 °C
+ pressing cylinder for hopper with four screw conveyors (WA)
+ Exciting shaft for hopper with four screw conveyors (WE)
+ Ultrasonic two-position material level sensor
+ Equipment for sludge briquetting
+ Catching tanks with pumps lowering the risk of contamination during manipulating with non processed chips and allows re-using of cooling liquid in machining centre
+ Safety fences
Videos